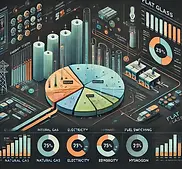
Energy Consumption Breakdown
Energy Breakdown of different configurations of flat glass decarbonisation
Energy Consumption and Emissions in Glass Furnaces
Glass production requires high-temperature furnaces to melt raw materials like silica, soda ash, and limestone. This analysis compares five furnace configurations based on energy consumption and COâ‚‚ emissions:
​
-
NGfur (Natural Gas Furnace) – Conventional fossil fuel furnace
-
NGOxyfur (Oxy-Fuel Furnace) – Uses oxygen for efficient combustion
-
Hybfur (Hybrid Furnace) – Partial Electrification
-
ELfur (Electric Furnace) – All electric furnace
-
H2fur (Hydrogen Furnace) – Uses hydrogen as a clean fuel
​
Energy Demand Components (GJ/tCOâ‚‚)
-
Q-Process – Thermal energy for glass melting
-
EL-Process – Electrical demand for furnace operations
-
EL-ASU – Electricity for oxygen production in oxy-fuel systems
-
EL-CPU – Power required by cryogenic CO2 capture
-
EL-CCS – Power Required by MEA based Carbon Capture
-
Q-CCS – Heat Required by MEA based Carbon Capture
-
Heat Recovered – Waste heat recovered for CCS
-
Power Generated – On-site power generation from heat recovery
​
Carbon Capture (CCS) Impact
CCS increases energy demand due to COâ‚‚ separation and compression but reduces overall direct and indirect emissions per ton of glass. This analysis highlights key decarbonization strategies in industrial glass manufacturing.
​